APQP (Perancangan Kualiti Produk Lanjutan)
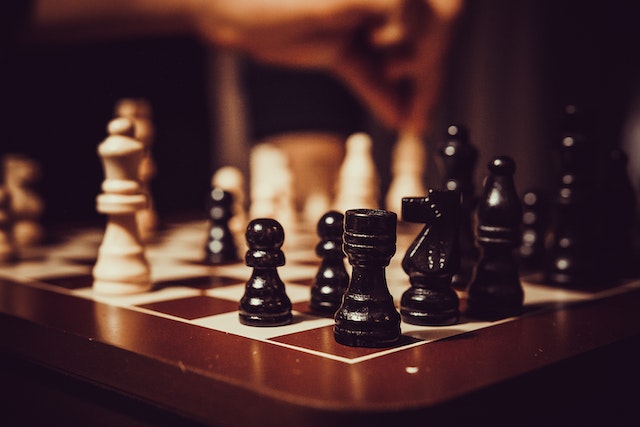
- 4487
- 312
- Ms. Santos Fritsch
Apa itu APQP?
APQP (Perancangan Kualiti Produk Lanjutan), Dalam "Perancangan Kualiti Produk Lanjutan" Sepanyol, adalah rangka prosedur dan teknik yang digunakan untuk membangunkan produk dalam industri, terutamanya dalam automotif.
Produk dan rantaian bekalan kompleks mempunyai banyak kemungkinan gagal, terutamanya apabila produk baru dilancarkan. APQP adalah proses berstruktur untuk reka bentuk produk dan proses, yang bertujuan menjamin kepuasan pelanggan dengan produk atau proses baru.
Pendekatan ini menggunakan alat dan kaedah untuk mengurangkan risiko yang berkaitan dengan perubahan dalam produk atau proses baru.
Tujuannya adalah untuk menghasilkan pelan standard untuk keperluan kualiti produk, yang membolehkan pembekal reka bentuk yang memenuhi pelanggan, memudahkan komunikasi dan kerjasama antara aktiviti yang berbeza.
Dalam proses APQP, peralatan pelbagai fungsi digunakan, yang melibatkan pemasaran, reka bentuk produk, pembelian, pengeluaran dan pengedaran. Proses ini digunakan oleh General Motors, Ford, Chrysler, dan pembekal mereka, untuk sistem pembangunan produknya.
Fasa APQP
APQP berfungsi sebagai panduan dalam proses pembangunan dan juga sebagai cara standard untuk berkongsi hasil antara pembekal dan syarikat automotif. Ia terdiri daripada lima fasa:
Fasa 1: Perancangan dan Definisi Program
Apabila permintaan pelanggan memerlukan pengenalan produk baru atau semakan yang sedia ada, perancangan menjadi tema utama, bahkan sebelum perbincangan mengenai reka bentuk atau reka bentuk semula produk.
Dalam fasa ini, perancangan bertujuan untuk memahami keperluan pelanggan dan juga jangkaan produk.
Aktiviti perancangan termasuk mengumpul data yang diperlukan untuk menentukan apa yang pelanggan inginkan dan kemudian menggunakan maklumat ini untuk membincangkan ciri -ciri produk.
Boleh melayani anda: Sektor Utama: Ciri -ciri, Aktiviti Ekonomi, KepentinganMaka anda boleh menentukan program kualiti yang diperlukan untuk mencipta produk seperti yang ditentukan. Hasil kerja ini termasuk reka bentuk produk, kebolehpercayaan dan objektif kualiti.
Fasa 2: Reka bentuk dan pembangunan produk
Tujuan fasa ini adalah untuk menyelesaikan reka bentuk produk. Berikut adalah penilaian daya maju produk. Hasil dari kerja dalam fasa ini termasuk:
- Semak dan pengesahan reka bentuk yang lengkap.
- Spesifikasi Bahan dan Keperluan Peralatan yang Ditakrifkan.
- Analisis kesan dan mod kegagalan reka bentuk selesai untuk menilai kebarangkalian kesalahan.
- Pelan kawalan yang ditubuhkan untuk penciptaan prototaip produk.
Fasa 3: Reka bentuk dan pembangunan proses pembuatan produk
Fasa ini memberi tumpuan kepada perancangan proses pembuatan yang akan menghasilkan produk baru atau bertambah baik.
Objektifnya adalah untuk mereka bentuk dan membangunkan proses pengeluaran, dengan mengambil kira spesifikasi dan kualiti produk, dan kos pengeluaran.
Proses ini mesti dapat menghasilkan jumlah yang diperlukan untuk memenuhi permintaan pengguna yang diharapkan, sementara kecekapan dikekalkan. Keputusan dalam fasa ini termasuk:
- Konfigurasi aliran proses lengkap.
- Kesan dan analisis kegagalan proses lengkap untuk mengenal pasti dan menguruskan risiko.
- Spesifikasi Kualiti Proses Operasi.
- Pembungkusan produk dan keperluan penamat.
Fasa 4: Proses dan Pengesahan Produk
Ini adalah fasa ujian untuk mengesahkan proses pembuatan dan produk akhir. Langkah -langkah termasuk:
- Pengesahan keupayaan dan kebolehpercayaan proses pengeluaran. Begitu juga, kriteria untuk menerima kualiti produk.
Boleh melayani anda: minat sederhana: elemen, cara mengira dan contohnya- Realisasi Pengeluaran Ujian Berjalan.
- Ujian produk untuk mengesahkan keberkesanan pendekatan pengeluaran yang dilaksanakan.
- Setuju pelarasan yang diperlukan sebelum beralih ke fasa seterusnya.
Fasa 5: Pelancaran, Penilaian dan Penambahbaikan Berterusan
Dalam fasa ini pelancaran pengeluaran skala besar berlaku, menekankan untuk menilai dan memperbaiki proses.
Di antara tiang fasa ini adalah pengurangan variasi proses, pengenalan masalah, dan permulaan tindakan pembetulan untuk menyokong peningkatan berterusan.
Terdapat juga pengumpulan dan penilaian maklum balas pelanggan dan data yang berkaitan dengan kecekapan proses dan perancangan kualiti. Keputusan termasuk:
- Proses pengeluaran yang lebih baik, dengan mengurangkan variasi proses.
- Peningkatan kualiti dalam penghantaran produk dan perkhidmatan pelanggan.
- Peningkatan kepuasan pelanggan.
Contoh
Di mana untuk menggabungkan APQP
- Pembangunan keperluan dari suara pelanggan, menggunakan pelaksanaan fungsi kualiti.
- Pembangunan pelan kualiti produk yang disepadukan dalam jadual projek.
- Aktiviti reka bentuk produk yang menyampaikan ciri khas atau utama untuk memproses aktiviti reka bentuk, sebelum membebaskan reka bentuk. Ini termasuk bentuk dan bahagian baru, toleransi yang lebih ketat dan bahan baru.
- Pembangunan rancangan percubaan.
- Penggunaan Kajian Reka Bentuk Formal untuk Memantau Kemajuan.
- Perancangan, pengambilalihan dan pemasangan peralatan dan peralatan yang sesuai, mengikut toleransi reka bentuk yang diberikan oleh sumber reka bentuk produk.
Boleh melayani anda: Institusi Ekonomi: Ciri, Contoh, Objektif- Komunikasi cadangan oleh kakitangan pemasangan dan pembuatan mengenai cara untuk memasang produk yang lebih baik.
- Penubuhan kawalan kualiti yang sesuai untuk ciri khas atau kunci produk atau parameter proses, yang masih menghadapi risiko kegagalan yang berpotensi.
- Melaksanakan kajian kestabilan dan keupayaan ciri khas untuk memahami variasi sekarang dan dengan itu meramalkan prestasi masa depan dengan kawalan proses statistik dan kapasiti proses.
Industri yang menggunakannya
Ford Motor Company menerbitkan manual perancangan kualiti maju pertama untuk pembekalnya pada awal tahun 80 -an. Ini membantu pembekal Ford membangunkan kawalan yang mencukupi untuk pencegahan dan pengesanan produk baru, dengan itu menyokong usaha kualiti korporat.
Pada akhir tahun 80 -an, pengeluar utama industri automotif di Amerika Syarikat menggunakan program APQ. General Motors, Ford dan Chrysler telah melaksanakannya dan kemudian melihat keperluan untuk bergabung untuk membuat pembekal mereka sebagai teras bersama prinsip perancangan kualiti produk.
Garis panduan ditubuhkan pada awal 90 -an untuk memastikan protokol APQP diteruskan dengan format piawai.
Wakil -wakil dari tiga pengeluar automotif dan Persatuan Amerika untuk Kawalan Kualiti mencipta sekumpulan keperluan kualiti, untuk mempunyai pemahaman yang sama tentang isu -isu yang saling berkait dalam industri automotif.
Metodologi ini kini juga digunakan oleh syarikat progresif untuk menjamin kualiti dan prestasi melalui perancangan.
Rujukan
- Perancangan Kualiti Produk Lanjutan. Diambil dari NPD-Solutions.com.
- Perancangan Kualiti Produk Lanjutan (APQP). Diambil dari kualiti -satu.com.